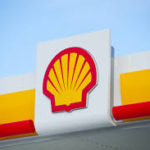
Shell Petroleum Development Company (SPDC)
Shell Petroleum Development Company (SPDC) is the pioneer and leader of the petroleum industry in Nigeria. We invest heavily in our employees, which is reflected in our industry-leading development programme and our commitment to see our employees’ ideas travel and come to fruition.
We are recruiting to fill the position below:
Job Title: Maintenance Work Preparer
Job Requisition ID: R127370
Location: Port Harcourt, Rivers
Job Type: Full time
Experience Level: Early Careers
What’s the Role?
- The Work Preparer role is critical to the effective productivity of the maintenance delivery team.
- The role will also ensure all maintenance/ operational activities are professionally and adequately planned and prepared for execution with the necessary procedures, documents, drawings, protocols in place as well as the timely supply of materials, services and logistics
- The role will be involved with various disciplines like mechanical, electrical or instruments but with a sound understanding of the production/operations & general maintenance processes.
- He/she is responsible for managing the work preparation backlog to acceptable levels such that all maintenance activities can be executed before the allowable finish date.
- May operate in one or more operations and maintenance disciplines e.g. Electrical, Mechanical, Instrument, Control Automation, Marine and Operations. This role will provide in-team subject matter expertise, peer guidance and support to their immediate teams, the Asset Production Units and any other teams.
- The job location for this role applies to Port Harcourt and Lagos.
Accountabilities
HSSE:
- Comply and enforce Shell Upstream lifesaving rules.
- Defines or adopts task lists which have the work executed at As Low As Reasonably Practicable (ALARP)
- Embed task risk assessment and required risk mitigation in the workpack, including required PPE consulting the permit issuing body
- Embed lifting and rigging plans for complex lifting and rigging jobs
Continuous Improvements:
- Initiate the update of Bill of Materials or Material Masters in case update is required
- Maintain the work-pack library to avoid necessary rework in future and enable continuous improvement of the work-pack
- Receive feedback from execution for improving the generic work-pack
Operational delivery:
- Deliver on time, with required quality control and continuous improvement.
- Perform regular quality checks and actively monitor progress.
- Maintain high staff utilization & productivity.
- Collaborate effectively within SNBO & other teams
Work Preparation:
- To work in collaboration with Field Discipline Maintenance Team in managing the work preparation to ensure the planning for Preventive Maintenances (PMs), Corrective Maintenances (CMs) and Turnaround activities are fully organized prior to execution, meeting Integrated Activity Plan (IAP) short and medium term planning KPIs.
- To collaborate and interface with Discipline Maintenance Technicians to finalize the scope of work, workpack manpower optimization and flawless workpack planning with the collaboration of Activity Owners, Operations team, Execution team and all relevant parties.
- Monitor the work preparation backlog, ensuring sufficient time for work pack development, materials supply and schedule float to allow timely execution of the job
- Develop the main steps (operations) in Computerized Maintenance Management System (CMMS – SAP) for executing the job, including mechanical (de)isolation, scaffold & insulation, cranes where required.
- Evaluate various options for repair & replacement and chooses the optimal one in relation to life cycle costs, reliability and safety. Where needed executes a field visit (virtually) to establish the local situation or (in case of remote locations) ask supervisor to send pictures/dimensions.
- Develop the purchase requisition for required materials and services.
- Liaises with the buyer on the required on-site date and clarifies specification where required.
- Define the initial earliest start date for the job accommodating the anticipated delivery time for materials and services
- Include the required drawings, pictures and documents in the work-pack, anticipating on the technician need during execution
- Add work Centre, number of resources required and estimated hours for each activity
- Include Quality Assurance/Quality Control (QA/QC) requirements and measurement protocols in the work-pack
- Seek feedback from execution to gain experience and update generic workpacks
- To enable the end-to-end process of material purchasing using Shell Companies in Nigeria Material Management “ways of working” and manage the Requisition-to-Pay (RtP) Process.
- To engage with Asset Field team on daily/weekly basis for CMMS-SAP Z1 notification approval meeting to screen through, review and challenge the necessity of all CMMS-SAP Z1 notification raised.
- To convert all approved Z1 notifications into work orders, making sure all necessary information related to the condition, maintenance operations, materials and resources required are incorporated into each work order.
- To take initiative in managing, from the initial stage, the cost of maintenance activities via identification of long lead material, resources required, and possible constraints that will be encountered in preparing, scheduling and execution of the said activities.
- To assist in Material Coding request as part as Bill of Material (BOM) improvement program & develop BOM for work preparation scope under the respective discipline.
- To complete work scoping template (including proposed execution strategy, preliminary man-hour estimation and populating Threats & Opportunity list) as well as to crosscheck the checklist of other Work Preparer as a mean to maintain quality of work.
- Review Field Status Review (FSR) daily and advise the team on potential non compliances for PM and CM orders.
- To ensure all Job Hazard Analysis (JHA), Hot-work Risk Assessment (HRA) and any other relevant work procedures (heavy lifting, complex and high-risk maintenance activities, etc.) are reviewed and analysed to be in accordance to Shell quality and safety requirement standard.
- To ensure all SIMOPS/SOP (Simultaneous Operation/Standard Operating Procedure) requirements are fulfilled and complied with
Ensure Compliance:
- Ensure that activities are executed in line with Shell’s policies; Technical Assist Organization (TAO) and Global SBO set standards including Data privacy/protection, HSSE&SP, Shell Asset Management System processes & others).
- Support timely preparation of terms of reference for proven work including scoping, Full-Time Equivalent (FTE) estimation & QA/QC.
What do we need from you?
- University Degree in any relevant discipline with a minimum 5 years of work experience in Operations & Maintenance/Production Operations/Engineering jobs in Oil & Gas/ Petrochemicals or any equivalent Industries. This should include a minimum of 3 years’ experience in performing/executing Maintenance activities in a Work Preparation/work Scheduler capacity (Candidates with HND with suitable work experience will also be considered)
- Strong Skill in equipment’s in his/her discipline e.g. Turbines, Generators, Pumps, Switch Gears, Transmitters, Export Pumps e.t.c
- Sound understanding of the production/operations & maintenance processes.
- Experience in leading teams in a virtual environment
- Experience of implementing change & continuous improvement projects.
- Experience in SAP Plant Maintenance (SAP-PM), as well as strong experience with MS Office (PowerPoint, Excel and others), is desirable
- Able to demonstrate in-depth technical knowledge & required skill sets for the role.
- Able to proactively manage stakeholder expectations
- Solid experience in Project management & Team Performance Management.
Behavioral Competences:
- Team Management & Leadership skills
- Strong communication skills
- The work preparer needs to be a self-starter, taking initiative and work without close supervision;
- Due to multiple/conflicting priorities, the candidate needs to be strong in prioritization, managing stakeholder expectations and be resilient under pressure.
- Should be able to guide the team and steer them through the tough/demanding situations and able to contribute hands on.
- Sound understanding of business/process workflow and having the mature mindset to deal and behave under tough/challenging situations.
- Passionately invest in coaching to enhance teams’ performance and capability for future roles. Hold honest performance conversations and intervene to address patterns of underperformance.
Application Closing Date
Not Specified.
Method of Application
Interested and qualified candidates should:
Click here to apply online